Excerpt: Guide – Heat pump knowledge in 4 modules
Module 3: Correctly plan and measure heat pumps.
1. Planning heat pump systems
However, everyday practice often demands even more from a specialist company. In contrast to combustion technology with energy sources such as oil, gas, wood or pellets, each degree Celsius in the thermodynamic cycle of a heat pump by and large plays a major role in the use of electrical energy. For example, 1 K higher evaporation temperature on the heat source side or 1 K lower condensation temperature at the heat sink bring about a 2 to 3 percent improvement in the COP of the heat pump. Expert knowledge is therefore required.
The planning of heat pump systems includes preliminary investigation, conceptual development and detailed planning. This should include hydraulic circuits, dimensioning of system components, documentation, commissioning of the system, instruction of the operator and also cost considerations.
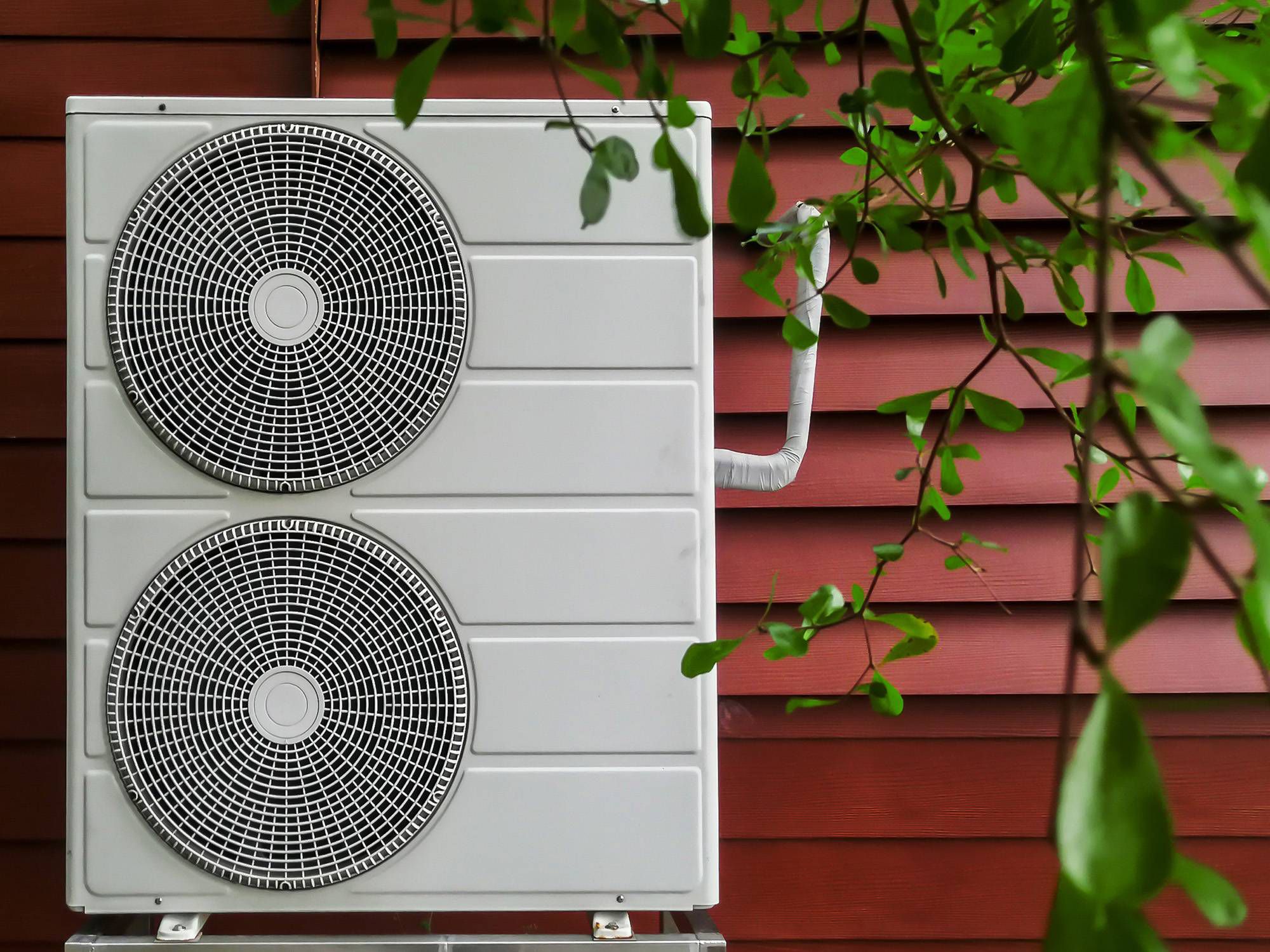
2. Practical knowledge for work in the field
Exact measuring values and expert knowledge form the basis for comprehensive system evaluation and correct adjustment of the refrigerant circuit of a closed split heat pump. This is the only way to record and evaluate crucial operating conditions or parameters.
Preparation
For commissioning and, primarily, in the event of servicing, it is crucial that the expert technician quickly obtains the most important system parameters of a refrigerant circuit. It is true that, to some extent, pressures and temperatures can be read out on modern heat pumps. However, it is only possible to be certain whether the displayed values are correct after a check. A manifold and a temperature measuring instrument are therefore indispensable tools when it comes to commissioning. However, measuring instruments are often exposed to mechanical and thermal stress in vehicles and on construction sites. The analog version, i.e. a manometer with mechanical pointers, has the disadvantage that crucial values such as subcooling and superheating cannot be read off directly. When calculating these values manually, there is always the risk of mathematical errors. In addition, so-called parallax errors, i.e. pressure value readout errors, can occur when interpreting the pointer position.
This is different with the digital manifold. Here, the pressures of the system and the associated temperatures can be recorded in parallel and very accurately to enable the superheating and subcooling to be determined. It is impossible to make either a parallax error or a mathematical error.
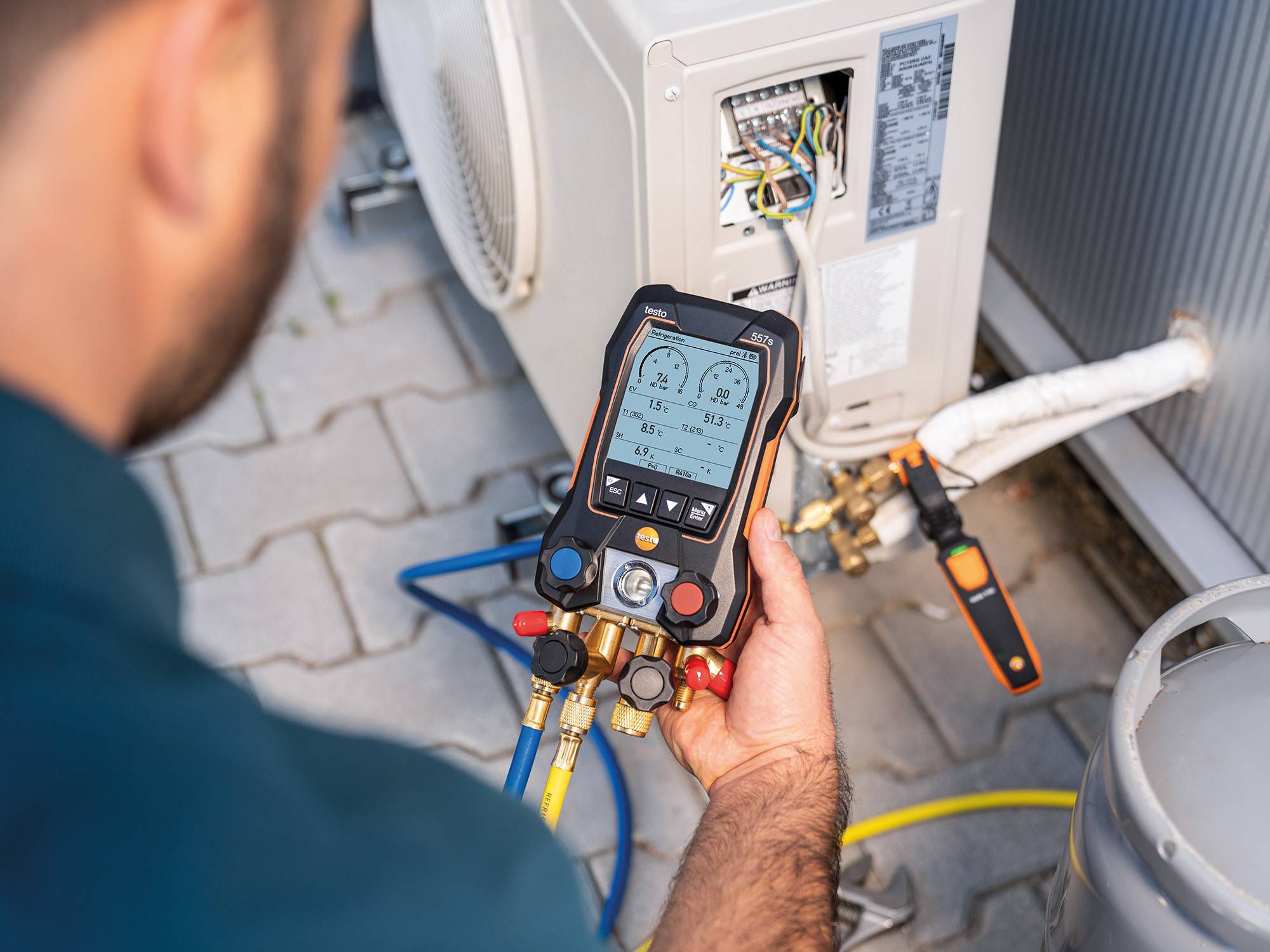
Initial commissioning
Once the heat pump has arrived and been installed, the cooling circuit of split systems must be completed. The correct choice of pipes to be used is taken from the current standards. This is because the material, wall thickness, toughness, corrosion and pressure resistance must be selected to match the refrigerant used. All soldered joints are connected leak-tight by brazing under inert gas (nitrogen) with copper or silver solder. This is followed by commissioning of the refrigerant circuit. The expert technician connects his/her digital manifold to the corresponding high-pressure and low-pressure connections of the heat pump. The red and blue hoses help the expert technician to keep track of where the pressure measurement is being taken. The third hose, which is usually yellow, is connected to the service port of the manifold. It is used initially to introduce dried nitrogen for the pressure or leakage test. It is also perfectly legitimate to remove the existing air from the pipelines and the heat exchanger beforehand using a vacuum pump and then introduce the dried nitrogen into the evacuated system.
Important subsequently: Gradually raise the test pressure to the calculated permissible overpressure. Only in this way can leaks due to pores or fine cracks in materials, weld seams and soldered joints be detected and eliminated in good time during subsequent operation. Other weak points for leaks are screw connections, valve stuffing boxes, measuring and monitoring devices and, paradoxically, seals of all kinds.
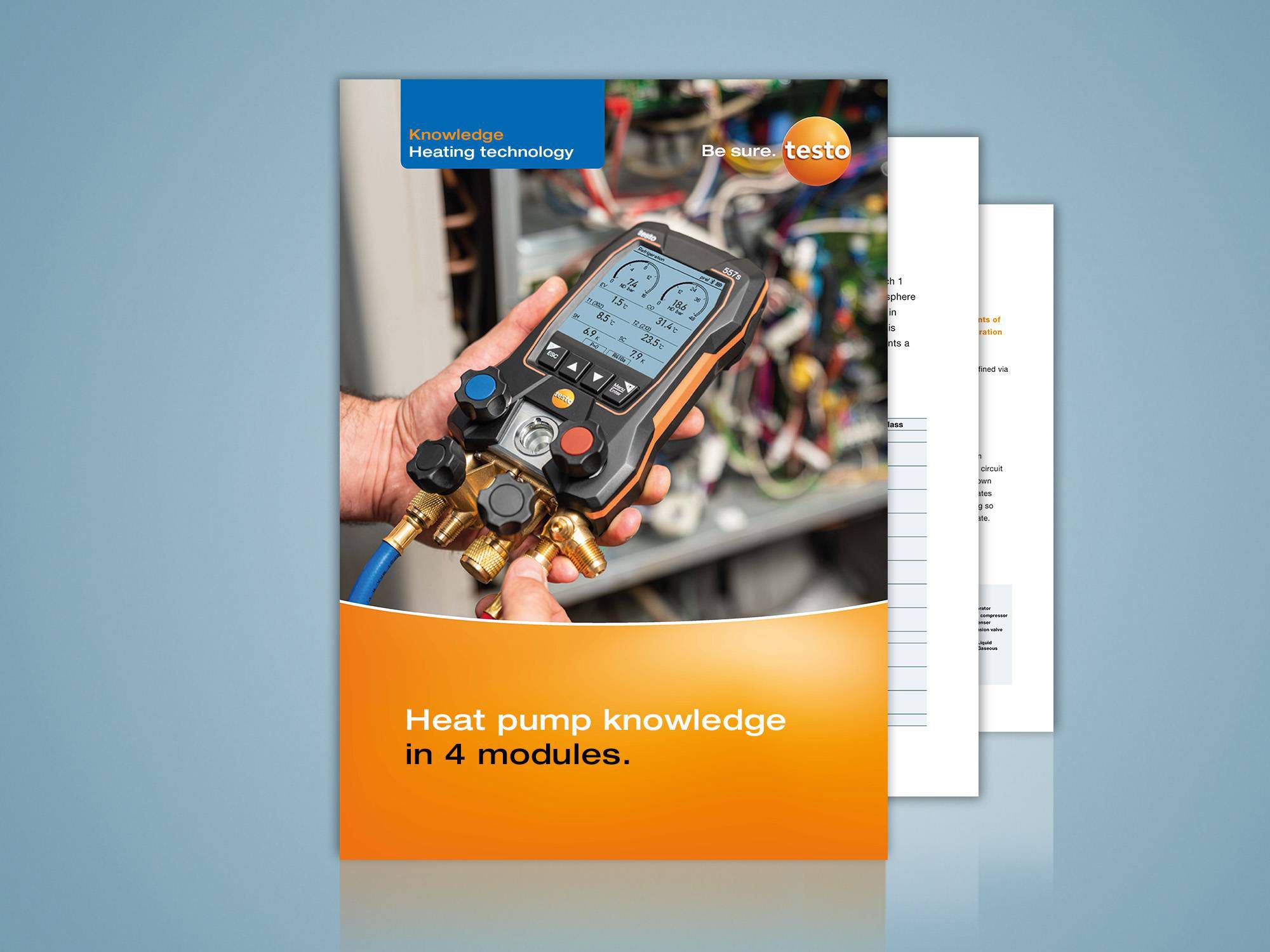
That was only a small excerpt. Would you like to find out more?
Request the complete guide now for free.
What you can expect to find in it:
Contents of the guide
Module 1: Understanding heat pumps
- Heat source - heat sink - system boundary
- Designs
- Modes of operation
- Practicable refrigerants
- GWP value
- Parameters for the efficiency of heat pumps
Module 2: Basic principles and main components
- Thermodynamics
- The four main components of the compression refrigeration circuit
- Other important components in the refrigerant circuit
Module 3: Planning and measuring correctly
- Planning heat pump systems
- Practical knowledge for work in the field
- Recording and evaluating important parameters
Module 4: Sound level
- The installation site
- Structure-borne sound
- Sound measurement
- Optical sound